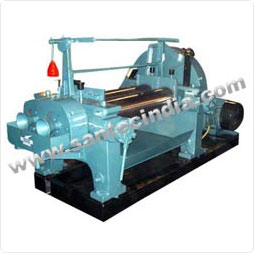
Rubber
processing machines offered by us comprise wide range of equipment and
machinery that is used in an industrial environment. The working of
different machines is given as follows:
Rubber Mixing Mills:
- In mill mixing, elastomer is first added to nip (Gap between two
rolls) that is open to about 6mm, at top of the rolls
- A band of elastomer passes through nip and is formed around the front
roll
- Depending on elastomer used, varying degrees of difficulty can be
encountered in forming band initially
- However, after few passes, a band will be formed that can be fed back
into nip continuously
- Elastomer is then cut back and forth twice to assure proper blending
as well s allow elastomer in bank to go through nip
- All dry ingredients, except fillers and cure system are then added to
nip
- Compound is then cut back and forth twice to assure good dispersion
of these dry ingredients throughout the batch
The next steps involves:
- Opening mill slightly and adding fillers slowly to batch that
prevents excessive loading of fillers at centre of roll several times
during this operation and thrown back into bank
- When most of fillers are mixed into compound, liquid plasticizers and
rest of fillers are added
- With filler visible, batch is cut back & forth twice more to
assure good distribution of fillers
- 'PIG'' roll batch & feed ''Pigs'' back into nip at right- angles
as part of cross-blending process
- Next step is to open mill more and add vulcanizing agents to batch
- When vulcanizing agents are well distributed, entire batch is cut
back & forth at least five times to assure thorough cross-blending,
before being sheeted off mill
Calander Machine Process :
- Calandering is efficient process for producing flat rubber sheets as
well as for frictioning, lamination, coating & embossing operation
- These machines are similar to rubber mill where rubber and other
components pass between two/ more metal rolls
- To produce product of controlled thickness, significantly higher
pressure is required, hence calander rolls, journals and frames are more
carefully designed and constructed
Rubber Extruders Process:
The extruders have two main functions - to pump rubber compounds through
barrel and to generate enough pressure in process to force material through
die to give required cross-sectional shape. The process includes
- Compound, usually in form of strip being fed at controlled rate into
extruder
- This imparts heat and some distributive mixing moves material along
machine and generates necessary pressure
- After leaving die, product is cured, cooled, cut to length &
packaged or coiled for transport to customers