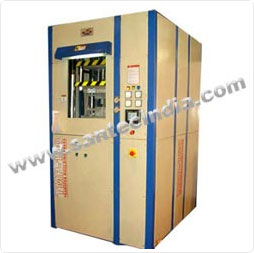
Today,
combination of injection molding press and twin-screw compounding extruder
represents new paradigm for processors, creating their own material whole
they mold them. Though these machinery systems are expensive, these are able
to successfully provide :
- New opportunities for materials cost savings
- Flexibility to tailor formulations for individual parts
With molder taking responsibility for raw materials and molded parts,
adding complexity to process multiplies number of variables to control. But
even then, these machines have established a growing niche and demand in the
market.
Presently, what started out a decade ago as way to reduce costs of molding
long-glass thermoplastic composites for structural automotive parts has
today also spread to non-automotive applications including other types of
compounding and alloying task. Some of the machine areas that got recent
upsurge in this field include:
- In-line compounding and injection molding
- Direct Long-Fiber (Reinforced) Thermoplastic processes (for in-line
compounding-and-molding)
To match these, either compression or injection processes are aimed at
assisting thermoplastic composites compete more cost-effectively with
thermoset SMC. With DLFT developed to be lower cost than glass-mat
thermoplastics (GMT) and long-fiber pellets produced by thermoplastic
pultrusion method, both GMT as well as long-fiber pellets need proprietary
processes to produce intermediate raw material in sheet/pellet form.
Further, GMT has additional disadvantage of producing substantial amounts of
scrap which cannot be reused in that process.
With first DLFT processes separating compounding and molding steps and
required manual/robotic transfer of hot compound to press, the latest step
introduced in this line is aimed towards integrating compounding and molding
on injection machine so as to effectively provide
- Greater automation
- Shorter cycles than can be achieved with compression molding